A New Generation of Sensors Is Here
. . . and it is ushering in the next industrial revolution. In the interconnected world of the Industrial Internet Things, some of the most important data about connected machines and equipment will come from sensors the likes of which we have not seen before. Here are some representative examples.
Share





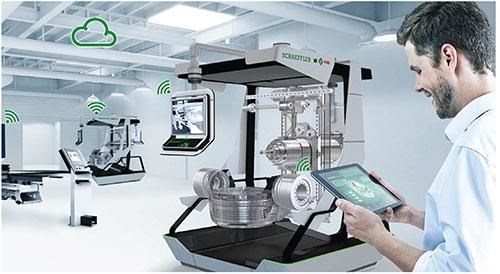
Schaeffler’s Machine 4.0 concept features a variety of sensors embedded in the bearing supports of a machining center. (Photo courtesy of Schaeffler group.)
A new generation of sensors is here and it is ushering in the next industrial revolution. In the interconnected world of the Industrial Internet Things, some of the most important data about connected machines and equipment will come from sensors the likes of which we have not seen before. Here are some representative examples.
Sensors in critical machine bearings. Because bearings and bearing supports are present in all of the moving parts of a machine tool that are critical to the machine’s functionality and machining accuracy, the condition of these components greatly influences the most vital performance characteristics of the machine tool. Detecting and measuring variables related to the condition of these bearings is a real boost to machine monitoring capability. Read how Schaeffler, a leading German supplier of industrial bearings, has embedded digital sensors in a machine tool to support Industry 4.0 concepts.
A sensory toolholder measures machining forces in real-time. The detects and measures the forces in torque occurring while a machining operation is underway. Strain gages embedded in the holder are connected to a transmitter that broadcasts the data wirelessly to a receiver and attached computer for analysis. We first saw this innovation at Westec 2015.
Detecting chips in a milling spindle. Grob’s chip-in-spindle detection system consists of a rotor and stator assembly that is integrated within the face of the spindle. Sensors in these components detect stresses that may indicate chip interference that occurs during an automatic tool change. Automatic monitoring of tool clamping to detect chip interference between the toolholder and the spindle has multiple benefits. It increases process stability; protects cutting tools and the machine; helps optimize machining processes; makes automatic tool changes more reliable; and prevents runout discrepancies that might result in machining errors or defective parts.
A low cost way of monitoring the temperature of machine tool components. As a summer project at the Advanced Manufacturing Resource Center in the UK, a chemical engineering student from the University of Sheffield developed the software and hardware for a wireless sensor network that can provide a drop-in solution for monitoring the temperature of multiple machine tools. His system uses the popular Arduino and Raspberry Pi platforms alongside inexpensive ZigBee radios which together provide a compact and low-cost solution for wireless data acquisition. . (Here is a PDF of the article if you are having trouble opening it in Chrome.)
Also, here's more about the importance of emerging sensor technology in the Industrial Internet of Things and Industry 4.0 (the fourth Industrial Revolution).
Related Content
-
ERP Provides Smooth Pathway to Data Security
With the CMMC data security standards looming, machine shops serving the defense industry can turn to ERP to keep business moving.
-
2 Secondary Coordinate Systems You Should Know
Coordinate systems tell a CNC machine where to position the cutting tool during the program’s execution for any purpose that requires the cutting tool to move.
-
Setting Up the Building Blocks for a Digital Factory
Woodward Inc. spent over a year developing an API to connect machines to its digital factory. Caron Engineering’s MiConnect has cut most of this process while also granting the shop greater access to machine information.