Five-Axis Blends Require Minding Ballnose Tolerances
Proper symmetry, expressed via the end mill’s diameter and radius tolerance, is critical to ensure smooth surface finishes during five-axis contouring operations.
Share






Die stamping components like this one are relatively rare at Legacy Precision Molds, which, true to its name, specializes mostly in plastic injection molds. However, 3+2 toolpaths like the one used for this part are quite common—more common, in fact, than full simultaneous contouring. Only when the shop made that leap (from 3+2 to full five) did it discover a need for new ballnose tooling.
At first, making the leap from 3+2 to full five-axis contouring didn’t look like a very promising development for (Grand Rapids, Michigan). Nine months after installing their first five-axis, a DMU 50 from , Tyler Vanree and the rest of the crew at this 14-employee shop were struggling to avoid blend lines on parts that would have posed no problems machining smooth on simpler equipment. As it turned out, however, the problem didn’t have anything to do with the shop’s newest machine, nor with its operators or programmers, VanRee says. Rather, the problem was with the cutting tools.
Not that there was anything wrong with those tools intrinsically. After all, ballnose cutters identical to those on the new five-axis machine had been employed on countless three-axis jobs over the years without issue. Yet, those designs simply wouldn’t stand up to the demands posed by five-axis machining, which requires a highly symmetrical ballnose profile to ensure smooth, line-free surfacing. These days, shop personnel insist that all tools employed for contouring have diameter and radius tolerances within ±0.0005 inch. At that level of precision, personnel can rest assured that machining will proceed exactly as planned even if different portions of the cutting edge engage the material at different points along the tool path.
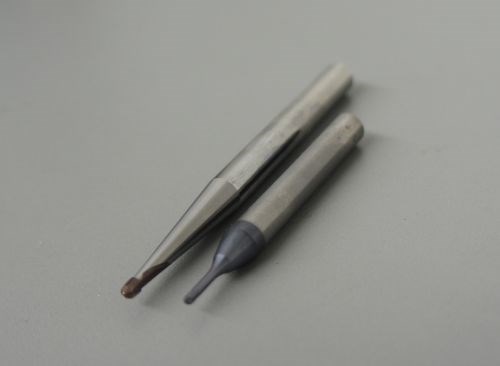
Beyond tight tolerances, the shop appreciates the fact that VHM ballnose end mills are available with various neck lengths. This attribute saves time previously spent grinding shanks back, whether for rigidity, to ensure a tool fits in its heat-shrink holder, to better access features like vertical walls, or any of the above.
Of course, other shops with other priorities and specialties might specify different tolerance requirements for ballnose cutters. Whatever the level of precision, Vanree emphasizes the importance of considering both tolerance figures—that is, both radius tolerance and diameter tolerance—and checking the math. Although these dimensions are interlinked (that is, one figure depends largely on the other), cutting tool manufacturers often specify tighter tolerances for ballnose radii than for diameters.
“If you had a 0.25-inch-diameter cutter and swung a perfect radius from one side to the other, that radius would measure 0.125 inch—half the diameter,” Vanree explains. “If you shrink the diameter, the radius will shrink with it. That’s why having looser tolerance on the diameter than the radius can complicate things when you’re trying to program the toolpath. So, we try to find tools where diameter and radius tolerance figures match up as well as possible.”
Legacy Precision Molds has learned plenty more lessons since bringing in its first five-axis machining center. To learn more, keep an eye on this blog and for our February issue, which will include a feature article on the shop’s experience.
Related Content
Orthopedic Event Discusses Manufacturing Strategies
At the seminar, representatives from multiple companies discussed strategies for making orthopedic devices accurately and efficiently.
Read MoreHow to Mitigate Chatter to Boost Machining Rates
There are usually better solutions to chatter than just reducing the feed rate. Through vibration analysis, the chatter problem can be solved, enabling much higher metal removal rates, better quality and longer tool life.
Read More6 Machine Shop Essentials to Stay Competitive
If you want to streamline production and be competitive in the industry, you will need far more than a standard three-axis CNC mill or two-axis CNC lathe and a few measuring tools.
Read MoreInside a CNC-Machined Gothic Monastery in Wyoming
An inside look into the Carmelite Monks of Wyoming, who are combining centuries-old Gothic architectural principles with modern CNC machining to build a monastery in the mountains of Wyoming.
Read MoreRead Next
AMRs Are Moving Into Manufacturing: 4 Considerations for Implementation
AMRs can provide a flexible, easy-to-use automation platform so long as manufacturers choose a suitable task and prepare their facilities.
Read MoreMachine Shop MBA
Making Chips and 91ÊÓÆµÍøÕ¾ÎÛ are teaming up for a new podcast series called Machine Shop MBA—designed to help manufacturers measure their success against the industry’s best. Through the lens of the Top Shops benchmarking program, the series explores the KPIs that set high-performing shops apart, from machine utilization and first-pass yield to employee engagement and revenue per employee.
Read More