How to Calculate Wheel Life in a Creep-Feed Grinding Process
For non-continuous-dress creep-feed grinding, the calculation is straightforward. For continuous dressing, the calculation has more steps, but in either case, it is possible to manage the cost of grinding by predicting the life of the wheel.
Share




Creep-feed grinding is a form of precision grinding that has proven to be a great development in modern grinding technology. As compared to conventional surface grinding, it provides excellent potential to increase productivity and improve dimensional accuracy. Creep-feed grinding is characterized by heavy stock removal, frequently greater than 0.030 inch or 2 mm of stock removal per pass. The purpose of this article is to demonstrate the calculation of wheel life in creep-feed grinding. Calculating wheel life is essential for forecasting wheel usage and the abrasive costs associated with a grinding process. In order to calculate the wheel life, it is essential to know which dressing methodology is being used. There are two types of dressing methods that can be used in a creep-feed grinding process:
1. Non-continuous dressing, in which an overhead or table-mounted diamond dresser is used to plunge or traverse-dress the form into the wheel intermittently. The dress amount is programmed in inches or millimeters.
2. Continuous dressing, which is beneficial in large-quantity production in materials that are difficult to machine or grind. The continuous dressing enables the grinding wheel to stay sharp constantly, while maintaining intricate forms. Continuous-dress creep-feed grinding uses an overhead diamond dressing roll to plunge dress continuously during the grinding cycle. The dress amount is programmed in inches or millimeters per revolution of the wheel.
Wheel Life Calculation in Non-Continuous-Dress (NCD) Creep-Feed Grinding
Wheel life in NCD creep-feed is the usable abrasive divided by the dress amount per part. Here are some representative process data to illustrate a NCD creep-feed grinding calculation:
- Max. diameter of wheel: 16 inch
- Min. diameter of wheel: 10.5 inch
- Usable abrasive (radial): (16 – 10.5) / 2 = 2.75 inches
- Dress amount per part (radial): 0.006 inch
Wheel life is then 2.75 / 0.006 = 458 parts per wheel.
Wheel Life Calculation in Continuous-Dress (CD) Creep-Feed Grinding
Wheel life in CD creep-feed grinding is the usable abrasive divided by wheel wear per grind cycle. Here is how to calculate wheel wear per grinding cycle:
1. Wheel Speed
Most creep-feed machines have a variable-speed motor to ensure that the speed of the grinding wheel in surface feet per minute (sfpm) remains constant throughout the life of the wheel. Constant sfpm is essential to ensure optimal wheel life. Decreased sfpm will result in fewer cutting edges engaged per unit time of grinding, causing higher load on each individual grain. This results in increased friability of grains, causing premature wheel breakdown. As the wheel gets smaller, the sfpm stays constant, so the revolutions per minute (rpm) will increase. The dressing roll feeds a certain depth into the wheel per revolution. Hence, the dressing amount increases as the wheel gets smaller. Therefore, to calculate average wheel life, we account for rpm at half the wheel diameter:
Average rpm = sfpm / (π/12 × DH)
Wheel diameter at half of wheel life (DH) (in inches) = Start Dia. – ((Start Dia. – Min. Dia.) / 2)
2. Wheel Travel
In CD creep-feed grinding, the diamond roll starts dressing the wheel as soon as the grinding wheel starts moving. Therefore, the wheel in-feed length, popularly known as wheel travel, is taken into consideration for calculating the dress amount per cycle. As the wheel gets smaller, the amount of clearance necessary to avoid a crash between the wheel and the part decreases. Most machines automatically take that into consideration. As the wheel gets smaller, the starting position of the wheel is closer to the workpiece, which means the wheel travel decreases. Therefore, the half-life wheel diameter is used to calculate the average wheel life.
Three entities make the wheel travel:
- Grind length of the workpiece
- Half-chord length at full arc of contact (L)
- Security length
In order to calculate the half-chord length at full arc of contact, we need to know the depth of cut (DOC) of the workpiece and the radius (r) of the wheel.
We can use a basic geometrical formula derived from the Pythagorean Theorem utilizing the DOC, radius of the wheel and the half-chord length at full arc of contact to calculate in-feed length (L). See figure:
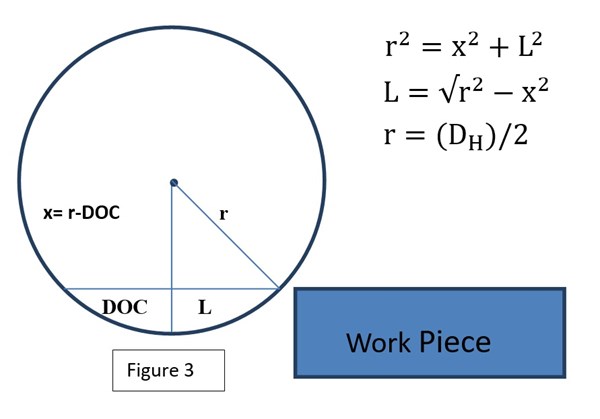
3. Wheel Wear
The formula to calculate the wheel wear is:
Wheel Wear per Grind Cycle = Continuous Dress Amount per Revolution of the Wheel (CD) × rpm × Wheel Travel / Table Speed
4. Wheel Life
Now we can calculate the wheel life:
Wheel Life = Usable Abrasive / Wheel Wear per Grind Cycle
Where…
Usable Abrasive = (Max. diameter of wheel – Min. diameter of wheel) / 2
Example
Assume these data for a representative CD process:
- Max. diameter of wheel: 16 inches
- Min. diameter of wheel: 10.5 inches
- Wheel speed: 2,500 sfpm
- CD amount per revolution: 0.00002 inch
- Table speed: 8 ipm
- Grind length: 2 inches
- Security length: 0.1 inch
- Depth of cut: 0.075 inch
Therefore:
DH = 16 – ((16 – 10.5) / 2) = 13.25 inches
r = 13.25 / 2 = 6.625 inches
x = 6.625 – 0.075 = 6.55 inches
L = √(r^2 – x^2) = 0.99 inch
Total Travel = 2 + 0.99 + 0.1 = 3.09 inches
rpm = (2,500 × 12) / (13.25 × π) = 721
Wheel wear per grind cycle = (0.00002 × 721 × 3.09) / 8 = 0.00557 inch
Usable abrasive = (16 – 10.5) / 2 = 2.75 inches
Wheel life = 2.75 / 0.00557 = 493 parts/wheel
Conclusion
This article describes how the life of a wheel can be determined in a creep-feed grinding operation. Calculating wheel life is essential for forecasting wheel usage and the abrasive costs associated with a grinding process. In order to calculate the wheel life, it is essential to know which dressing methodology is being used. Wheel life is calculated by dividing the usable abrasive by wheel wear. Calculating wheel wear in a continuous-dress creep-feed grinding operation is complicated. The dressing amount is programmed per revolution of the wheel. The number of revolutions the wheel completes per cycle is dependent on the wheel diameter, wheel speed in sfpm, the grinding length, the depth of cut and the table speed.
Related Content
How to Evaluate Measurement Uncertainty
Manufacturing and measurement are closely coupled. An important consideration for the use of measurement results is the associated measurement uncertainty. This article describes common metrology terms and provides an example uncertainty analysis.
Read More4 Rules for Running a Successful Machine Shop
Take time to optimize your shop’s structure to effectively meet demand while causing the least amount of stress in the shop.
Read MoreCustom Workholding Principles to Live By
Workholding solutions can take on infinite forms and all would be correct to some degree. Follow these tips to help optimize custom workholding solutions.
Read MoreTips for Designing CNC Programs That Help Operators
The way a G-code program is formatted directly affects the productivity of the CNC people who use them. Design CNC programs that make CNC setup people and operators’ jobs easier.
Read MoreRead Next
Last Chance! 2025 Top Shops Benchmarking Survey Still Open Through April 30
Don’t miss out! 91ÊÓÆµÍøÕ¾ÎÛ's Top Shops Benchmarking Survey is still open — but not for long. This is your last chance to a receive free, customized benchmarking report that includes actionable feedback across several shopfloor and business metrics.
Read MoreMachine Shop MBA
Making Chips and 91ÊÓÆµÍøÕ¾ÎÛ are teaming up for a new podcast series called Machine Shop MBA—designed to help manufacturers measure their success against the industry’s best. Through the lens of the Top Shops benchmarking program, the series explores the KPIs that set high-performing shops apart, from machine utilization and first-pass yield to employee engagement and revenue per employee.
Read MoreAMRs Are Moving Into Manufacturing: 4 Considerations for Implementation
AMRs can provide a flexible, easy-to-use automation platform so long as manufacturers choose a suitable task and prepare their facilities.
Read More