Machine Monitoring Proves Its Worth
These three short case histories document the value of implementing a manufacturing execution system for machine monitoring. In each case, MERLIN hardware and software modules from Memex Automation led to productivity gains and improved overall equipment effectiveness (OEE).
Share





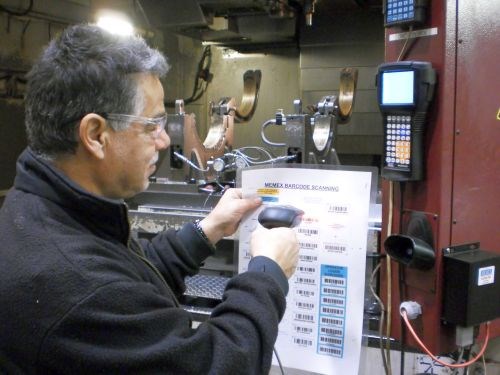
Implementing a manufacturing execution system to monitor machine performance helped Magellan Aerospace improve OEE on critical production cell. Image courtesy of the company.
The experiences of these three machining companies document the value of implementing a manufacturing execution system for machine monitoring. In each case, MERLIN (Manufacturing Enterprise Real-time Lean Information Network) hardware and software modules from led to productivity gains and improved overall equipment effectiveness (OEE).
- of Carlton Place, Ontario, was able to make fact-based improvements to shopfloor systems and reorganize workflows and resources to generate an increase in OEE of 105 percent in one year.
- of Kitchener, Ontario, went from a 36.9 percent OEE rating to a 85 percent OEE rating, and determined that a cell of three machines need not be expanded to a fourth machine.
- of Edmonton, Alberta, has made several advantageous changes to their tooling systems and can readily test the real cost of benefits of suggested new machining procedures.
For the complete case histories click here.
Related Content
-
Manufacturer, Integrator, Software Developer: Wolfram Manufacturing is a Triple Threat
Wolfram Manufacturing showcased its new facility, which houses its machine shop along with space for its work as a provider of its own machine monitoring software and as an integrator for Caron Engineering.
-
Precision Shop Adopts Machine Monitoring, Boosts Revenue
Adopting machine monitoring helped LeClaire Manufacturing boost its vertical CNC utilization rates 38 percentage points and gain millions in revenue.
-
5 Stages of a Closed-Loop CNC Machining Cell
Controlling variability in a closed-loop manufacturing process requires inspection data collected before, during and immediately after machining — and a means to act on that data in real time. Here’s one system that accomplishes this.