Major Tool & Machine Continues Major Upgrades
This Indianapolis shop’s extensive series of machine tool retrofits sheds light on how to best approach these projects.
Share




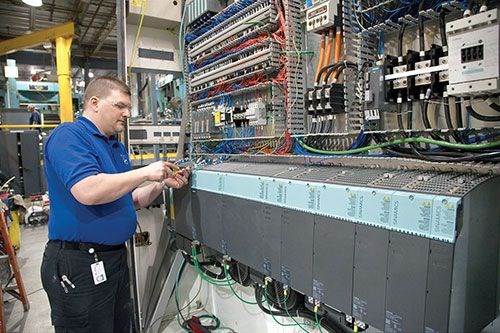
The DSI machine project is the latest in an extensive series of retrofits at Major Tool & Machine. Here, Scott Elder of Indiana Automation installs wiring at the electrical enclosure of one of the previously upgraded machines, a Cincinnati U5.
is no stranger to extensive retrofit projects, and the company’s latest order is no exception. Set for completion in 2015, the job involves equipping a DSI (Dorries Scharmann) turn-mill gantry machine with not only a new Siemens CNC and drive system, but also a new cross-saddle, ram, and five interchangeable cutting heads, among other components. This work follows close on the heels of a series of similar projects that the shop began to undertake in 2010, and it can be similarly informative for manufacturers considering their own rebuilds.
As detailed in this article from our May issue, these previous projects demonstrate that retrofits provide the opportunity to not just restore machines to like-new condition, but also to add new capabilities. Just as importantly, the article describes why rebuilding MTM’s old machines would have been a complicated, involved process even if the company had less lofty goals. In fact, anything less than a total motion system upgrade wouldn’t even have been an option.
The DSI machine rebuild also demonstrates the need to plan around downtime. The project is part of a multi-million dollar order from MAG IAS that also includes two new machine tools: A VTC 2500 and a U5 XL 2500 universal portal mill with turning capabilities. The rail-type U5 XL 2500, the newest and largest model of the U5 portal mill series, will initially replace production capacity during the rebuild the DSI machine. “This is an extremely complex project that involves much more than simply adding machine tools, because it is critical that we maintain our large-part mill/turn capacity when the DSI machine goes offline,” says Steve Weyreter, chairman and CEO of MTM. “Part of our reputation is based on the depth of our capacity, so coordination and timing are vital when we take a critical machine offline.”
Here are more specific details on the new machines and what the DSI machine retrofit project will entail.
Related Content
-
How to Determine the Currently Active Work Offset Number
Determining the currently active work offset number is practical when the program zero point is changing between workpieces in a production run.
-
6 Variations That Kill Productivity
The act of qualifying CNC programs is largely related to eliminating variations, which can be a daunting task when you consider how many things can change from one time a job is run to the next.
-
4 Commonly Misapplied CNC Features
Misapplication of these important CNC features will result in wasted time, wasted or duplicated effort and/or wasted material.