The Intersection of Work, Play, Technology and Independence
The February issue dives into digital technologies that not only streamline production, but make a tangible difference in people’s lives.
Share




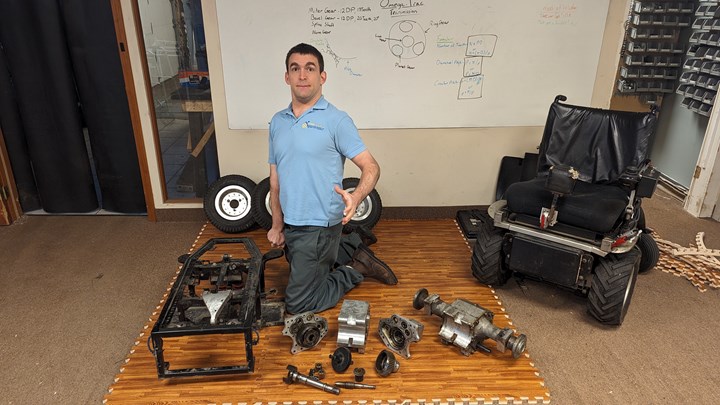
Devin Hamilton, owner and founder of RapAdapt, disassembles a power wheelchair and makes plans for improvements to the frame, suspension, and drive system. Photo Credit: RapAdapt
Technology serves us well, perhaps best, when it facilitates creativity and invention. In the world of metalworking and CNC machining, we see this kind of facilitation made possible through digital tools such as CAD and CAM software that enable ideas to manifest into real-world solutions. When we are successful, we celebrate the solutions and innovations that inspire us, assist us, teach us, entertain us, or allow us to push the boundaries of human creativity.
We sometimes couch our pursuits and aspirations in phrases like “making a difference” and “making the world a better place,” worthy goals that are agnostic to our abilities or means or chosen professions. But truly worth celebrating are those who make the aid and assistance of others their life’s pursuit — people who work to make the world the better place not in the abstract, but tangibly and directly, one life at a time.
This month’s cover feature by Editor Emeritus Mark Albert tells just such a story. On one level, Albert tells the story of a custom manufacturer called that uses integrated CAD/CAM to design and produce things that, as he puts it, “help people work, play and go about their lives with more independence.” On this level, it is a story that explores the relationship between ideas and reality through a lens of technology. But, as you’ll read, the story of RapAdapt is about much more than only the digital manufacturing tools.
RapAdapt is the brainchild of Devin Hamilton, a man who studied mechanical engineering at the Rochester Institute of Technology before opening his shop in 2016. The company focuses on custom solutions for people with disabilities, including power wheelchairs and wheelchair accessories, custom utensils and other mass-market products that Hamilton adapts for people on an individualized basis. While RapAdapt has been around for just eight years, Hamilton has been doing this kind of work for most of his life.
Since early childhood, Hamilton has been living with cerebral palsy, a neurological condition that affects the part of the brain that controls muscle movement. Growing up on a farm with a supportive family in upstate New York, Hamilton and his father began modifying wheelchairs when Hamilton was just three years old, creating tools and making modifications that allowed him to be an active part of life on the farm. This work in his youth formed a powerful connection to design and engineering now fully realized at Hamilton’s company.
I recently spoke with Devin Hamilton along with his weekend engineering assistant at RapAdapt, Mike Partridge. (You’ll meet Hamilton’s full-time engineering assistant, Alex Peña, in Albert’s story.) Hamilton is so accustomed to the adaptations that he’s manufactured for everything from his computer to his chair to his CNC machines, that it’s hard to name them all. He works seven days a week, a feat made possible with the recent addition of Partridge, a high school engineering and robotics teacher who responded to Hamilton’s Craigslist ad seeking a weekend assistant. When one of Hamilton’s new clients expressed surprise when he scheduled their first consultation on a Saturday, he half-jokingly replied, “My disability doesn’t take the weekends off, does yours?”
In addition to RapAdapt, Hamilton is working with the to build what he calls “an extremely robust open-source wheelchair.” He’s speaking at this year’s on February 12 in Dallas, Texas, where he’ll show how he uses eye-tracking technology to use SolidWorks and take advantage of the platform’s efficiency-boosting tools.
CAD and CAM software makes other notable appearances in this issue of 91ÊÓÆµÍøÕ¾ÎÛ, including a feature article by Associate Editor Nathaniel Fields about Napolean Machine, a large-part welding and CNC machining shop in Ohio. Fields examines how the shop takes advantage of Mastercam’s Dynamic Motion toolpaths to produce consistent chip thickness and chip load, helping the company produce nearly 800 parts per year for M1 Abrams tanks. Fields also dives into the world of off-roading in his story about a company that brought machining of its off-road parts and components in-house with the help of CAMWorks Simulator. The software, integrated with SolidWorks, automatically updates the G code if shop programmers need to tweak the model after running a simulation. Prior to this move, the shop was spending up to $45,000 per month on outsourced machining.
Senior Editor Julia Hider and Associate Editor Evan Doran round out the issue with two contributions to our new feature sections. Check out Hider’s installment of “The Cut Scene,” which examines a 3D-printed steering knuckle for an electric dune buggy that was designed with downstream operations in mind, including the CNC machining of critical surface features. Also, check out Doran’s interview with Kaci King, West Ohio Tool’s second-generation owner and CEO, who talks about reestablishing the company’s core values after stepping into her leadership role. Later, in this month’s “How I Made It,” King offers these parting words of wisdom: “Follow your gut, always,” she says. “Sometimes we’re not good at listening to it. But at the end of the day when it’s quiet and you gain clarity, it’s never wrong.”
Related Content
Building A Powerful Bridge from the CAM Programmer to the Shop Floor Operator
SolidCAM for Operators provides a powerful bridge from CAM programming to the shop floor to best streamline the machine shop process with its CAM part simulation. It provides a clear picture to the operator for setup and prove-out, enables minor G-Code changes and avoids crashes, broken tools and scrapped parts.
Read MoreCutting Part Programming Times Through AI
CAM Assist cuts repetition from part programming — early users say it cuts tribal knowledge and could be a useful tool for training new programmers.
Read MoreLarge-Format Machining With Small Cutting Tools and Dynamic Motion
Napoleon Machine, a defense contractor that provides parts for the M1 Abrams tank, recently took advantage of a CAM feature that allowed the company to streamline its cutting strategies and program offline. Here’s how the shop cut cycle times nearly in half with its large-format five-axis machining operations.
Read MoreHow Integrated CAD/CAM Transforms Inventions Into Products
The close connection between CAD and CAM is what links creative ideas to practical production for this unique custom manufacturer.
Read MoreRead Next
An Open Letter to Kids About Machines and the World of Making Things
This is an open letter to middle- and high-school students about choices they’ll soon face. It is also an introduction to Career and Technical Education (CTE), the world of CNC machining, and a reminder that there are options outside of the traditional four-year college path.
Read MoreThe Resurgence of 'Shop Class' in American High Schools
From the 1990s through the 2010s, most traditional “shop classes” disappeared from middle schools and high schools across the U.S. — one of the many issues that helped create today’s skilled labor shortage in metalworking and CNC machine shops. Here’s one solution that deserves more attention.
Read MoreLast Chance! 2025 Top Shops Benchmarking Survey Still Open Through April 30
Don’t miss out! 91ÊÓÆµÍøÕ¾ÎÛ's Top Shops Benchmarking Survey is still open — but not for long. This is your last chance to a receive free, customized benchmarking report that includes actionable feedback across several shopfloor and business metrics.
Read More