You Are Not Spending Enough on Gaging
Is there an intuitive ratio shaping shops’ perceptions of how much gaging capacity is appropriate for their machining capacity? Much has changed; that ratio might need to be reconsidered.
Share




Many shops today have an outmoded feel for how much inspection and measurement capacity and hardware is appropriate for the number of machine tools they have.
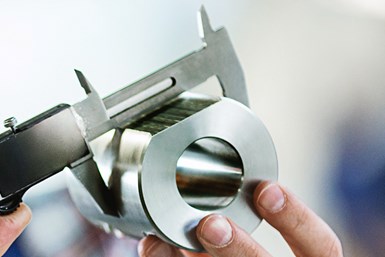
I can’t prove that assertion for any given shop or identify which shops those are, but this sense ties together many observations I’ve heard from shops repeatedly, including these:
- When shops use machine monitoring systems to track and diagnose productive in-cut time, these reports frequently seem to reveal inefficiencies related to gaging as the reason why potentially productive machine tools are kept waiting. In one example, a given machine tool’s output was notably improved just by moving the table closer on which a needed gage was located.
- Gaging is often noted as the peril of lights-out machining. That is, if the shop really becomes effective at continuing production through the night, “then we are going to have all those parts to inspect in the morning.”
- For otherwise lean, clean and airy shops, the one place work-in-process inventory most frequently still seems visible is on the racks in or near the inspection room.
That our intuitive ratio of machining capacity to measurement capacity might bear examination stands to reason. A single machine tool today can do more. A precise multitasking machine consolidating what might have been the work of several setups into one can reduce the number of features that need to be inspected, but not to the same proportion that it reduces the number of setups. The machine’s one setup generates a larger number of critical features than a setup on a simpler machine. The proportion of measurement per machine tool therefore goes up.
Lights-out machining then takes this even farther. The observation about “parts to inspect in the morning” is not wrong; it is an accurate observation of one of the critical requirements of leveraging unattended machining capacity. Namely, the automated machining either must be paired with the capacity to quickly inspect all the parts it produces, or else the inspection process has to be automated to the same extent as machining. Either way, gaging capacity must increase.
But there is something else going on here, something more fundamental. For multiple decades now, machining businesses in the United States have been migrating toward higher levels of value in what they produce. More recently, OEMs have been more strongly leaning toward third-party quality standards (AS 9100, ISO 13485) as ways of certifying shops’ abilities to deliver this value. Meanwhile, design engineers have learned to leverage advanced manufacturing capability by specifying more complex components than in the past. All of this means that a machined part today tends to contain more value as it proceeds through the shop. The cost of scrap is higher. Measurement in machining has always safeguarded value, but today, the value that needs to be protected is higher than ever.
I will end on a couple of basic points about gaging that have always been true, but they are worth restating for any shop evaluating its gaging investment:
First, quality is a habit. And habits derive from what is easy, what is close at hand. This is the reason, for example, why a person wanting to eat better might move unhealthy food out of reach. In a machine shop, if gaging resources are ample, then this makes it easy for team members to fall into the habit of making measurements. By contrast, if gaging resources are a constraint, then this works against the habit for quality taking hold. Evading the constraint through workarounds, or by rationalizing that certain measurements can be skipped, will become the habit instead. One intangible argument for the investment in more gaging has to do with what it says to team members about the priorities of the culture.
Second, one of the areas in which the intuitive sense of productivity stands to be the most deceptive is in the observation of machining activity, cutting metal. The basic fact that the machine tools do the cutting informs our sense of proportionality in machines versus gages, because it appears to be the machines that are making the product. Of course, they are doing this. And yet the machine-shop adage, “If you’re making chips, you’re making money,” is at best incomplete. What makes money for a shop is making parts that meet measurement criteria acceptable to the customer. No machined part is done until a measurement validates the success of the work. In a very real sense, then, gaging legitimizes the work of a machine tool. As a shop’s machining capability stands taller and delivers more, gaging has to answer this advance.
Related Content
How to Evaluate Measurement Uncertainty
Manufacturing and measurement are closely coupled. An important consideration for the use of measurement results is the associated measurement uncertainty. This article describes common metrology terms and provides an example uncertainty analysis.
Read MoreParts and Programs: Setup for Success
Tips for program and work setups that can simplify adjustments and troubleshooting.
Read MoreMarathon Precision’s Engineering Playground: One Shop’s Secret to Sustaining High Tech, Low-Volume and High Morale
Half an airplane on the wall, a ten-foot metal dragon, and a full-blown recording studio might not scream “manufacturing efficiency,” yet Marathon Precision proves otherwise. Here’s how forging, complex CNC operations and staff-driven creative projects combine to fuel the shop’s productivity and profitability.
Read MoreThe Link Between CNC Process Control and Powertrain Warranties
Ever since inventing the touch-trigger probe in 1972, Sir David McMurtry and his company Renishaw have been focused on achieving process control over its own manufacturing operations. That journey has had sweeping consequences for manufacturing at large.
Read MoreRead Next
AMRs Are Moving Into Manufacturing: 4 Considerations for Implementation
AMRs can provide a flexible, easy-to-use automation platform so long as manufacturers choose a suitable task and prepare their facilities.
Read MoreLast Chance! 2025 Top Shops Benchmarking Survey Still Open Through April 30
Don’t miss out! 91ÊÓÆµÍøÕ¾ÎÛ's Top Shops Benchmarking Survey is still open — but not for long. This is your last chance to a receive free, customized benchmarking report that includes actionable feedback across several shopfloor and business metrics.
Read MoreMachine Shop MBA
Making Chips and 91ÊÓÆµÍøÕ¾ÎÛ are teaming up for a new podcast series called Machine Shop MBA—designed to help manufacturers measure their success against the industry’s best. Through the lens of the Top Shops benchmarking program, the series explores the KPIs that set high-performing shops apart, from machine utilization and first-pass yield to employee engagement and revenue per employee.
Read More