Ceratizit's FreeTurn Tooling Combines Different Cutting Edge Properties for Flexibility
Ceratizit’s FreeTurn tooling is designed to be used with its High Dynamic Turning (HDT) method, which is said to enable roughing, finishing, contour turning, face turning and longitudinal turning with a single tool.
Share





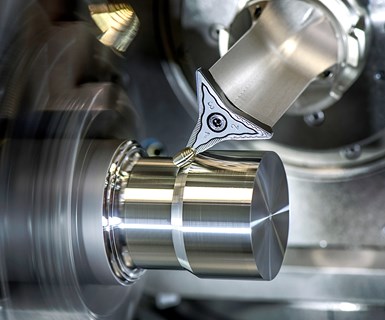
Ceratizit’s FreeTurn tooling is designed to be used with its High Dynamic Turning (HDT) method, which is said to enable roughing, finishing, contour turning, face turning and longitudinal turning with a single tool. FreeTurn tooling features a multi-sided insert at the cutting end of the slim shank. The insert, which screws into place, can have several cutting edges with different properties. This is said to allow for different angle points, corner radii or chipbreakers as well as different coatings and cutting materials. The tool can therefore be adapted to do specific machining requirements and provide savings in tool change times, tool magazine loadouts and overall tool costs, according to the company.
In the HDT method, the milling spindle is used to produce the corresponding approach angle to the workpiece. The use of the spindle drive in conjunction with the slim, axial design of FreeTurn tools is said to create a degree of freedom of 360 degrees without the risk of collision, the company says. Due to the rotation around its own tool axis, the cutting edge can be changed without interrupting the process. Additionally, the angle of approach is freely variable at any time and can even be changed while cutting, enabling flexible contouring and optimizing chip breaking for higher feed rates and longer tool life.
Related Content
-
Medical Shop Performs Lights-Out Production in Five-Axes
Moving to five-axis machining enabled this shop to dramatically reduce setup time and increase lights-out capacity, but success relied on the right combination of workholding and automation.
-
Lean Approach to Automated Machine Tending Delivers Quicker Paths to Success
Almost any shop can automate at least some of its production, even in low-volume, high-mix applications. The key to getting started is finding the simplest solutions that fit your requirements. It helps to work with an automation partner that understands your needs.
-
Shoulder Milling Cuts Racing Part's Cycle Time By Over 50%
Pairing a shoulder mill with a five-axis machine has cut costs and cycle times for one of TTI Machine’s parts, enabling it to support a niche racing community.