Siemens Updates CNC Control System for Enhanced Digitization
Siemens’ Sinumerik One CNC control system easily creates and works with digital twins of machine tools.
Share





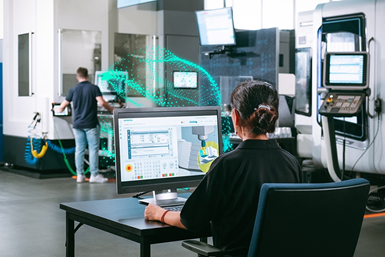
Siemens is expanding its Sinumerik One “digital native” CNC. The new system software, Sinumerik V6.20, features new technology functions that are said to simplify machine tool operation, reduce machine wear and increase manufacturing productivity. The Sinumerik control system can be used for digital transformation in a highly productive, flexible and modular way.
With the new Y-turning function, Sinumerik One can be used for machines that turn from the Y-axis, enabling up to 3X the feed rate. New tool types were created for this purpose and all turning functionalities and cycles were adapted for these tools.
The Advanced Rapid Movement function is also one of the innovations in this new technology. It enables time-optimized movement, which means faster movements take place between machining operations. The part program does not require a change. Overall, machining can be up to 10% faster, according to Siemens. The function can be implemented in tandem with the machine builder.
With Reduced Dynamic Mode, there is now a CNC function that actually reduces wear on the machine and increases its availability. The Numerical Control Kernel (NCK) function enables the machine tool builder to automatically transfer the machine to reduced operation if the axis becomes too warm. When the temp stabilizes, the machine can be returned to full load. In this way, the Reduced Dynamic Mode enables individual operation of machines in motion.
Additionally, hardware innovations for the Sinumerik One are designed to simplify operation. The new keyboards and machine control panels (MCPs) are now available from 15" to 24" to match the human-machine interface (HMI) design — and Simatic Industrial Thin Clients (ITCs) and industrial PCs are said to offer increased performance and a resolution up to 1920 × 1080 pixels.
The new MCPs are also integrated in the digital twin of Sinumerik One (Create and Run MyVirtual Machine), so that the appearance and operation correspond to the real CNC in every respect. In addition, the digital twin of Sinumerik One has been equipped with new features that simplify engineering and work preparation. The 3D option offers support for a second channel, and each tool can be assigned an individual color, so that the ablated surfaces are color-coded, depending on the tool used. The integration of the STEP format is an important new feature, especially for complex geometries of the clamping in a turning operation. Collision detection now also offers extensive functionalities such as the display of all collided bodies, NC program line and more, so the cause of collisions can be quickly investigated and fixed.
With its integrated Simatic S7-1500F PLC, Sinumerik One reportedly offers up to 10X faster PLC cycle times. With the Simatic S7-1500F PLC, Sinumerik One is now fully integrated into the Siemens TIA Portal engineering framework, enabling standardization of all engineering tasks for operators of larger plants. Sinumerik One is fully compatible with the previous Sinumerik 840D sl controller generation in terms of programming and operation, making the changeover to Sinumerik One more seamless.
With Sinumerik One, Siemens offers CNC technology that easily creates and works with digital twins of machine tools. Work preparation and engineering departments can also benefit from the digital twin. The user interface for Sinumerik One is said to enable convenient, flexible and efficient operation of machine tools across all machining technologies.
Related Content
2 Secondary Coordinate Systems You Should Know
Coordinate systems tell a CNC machine where to position the cutting tool during the program’s execution for any purpose that requires the cutting tool to move.
Read MoreCan AI Replace Programmers? Writers Face a Similar Question
The answer is the same in both cases. Artificial intelligence performs sophisticated tasks, but falls short of delivering on the fullness of what the work entails.
Read MoreTips for Designing CNC Programs That Help Operators
The way a G-code program is formatted directly affects the productivity of the CNC people who use them. Design CNC programs that make CNC setup people and operators’ jobs easier.
Read More4 Commonly Misapplied CNC Features
Misapplication of these important CNC features will result in wasted time, wasted or duplicated effort and/or wasted material.
Read MoreRead Next
Last Chance! 2025 Top Shops Benchmarking Survey Still Open Through April 30
Don’t miss out! 91ÊÓÆµÍøÕ¾ÎÛ's Top Shops Benchmarking Survey is still open — but not for long. This is your last chance to a receive free, customized benchmarking report that includes actionable feedback across several shopfloor and business metrics.
Read MoreMachine Shop MBA
Making Chips and 91ÊÓÆµÍøÕ¾ÎÛ are teaming up for a new podcast series called Machine Shop MBA—designed to help manufacturers measure their success against the industry’s best. Through the lens of the Top Shops benchmarking program, the series explores the KPIs that set high-performing shops apart, from machine utilization and first-pass yield to employee engagement and revenue per employee.
Read MoreAMRs Are Moving Into Manufacturing: 4 Considerations for Implementation
AMRs can provide a flexible, easy-to-use automation platform so long as manufacturers choose a suitable task and prepare their facilities.
Read More