Tongtai VTX Drilling, Tapping Machines Provide High Precision
With rapid traverse speeds ranging to 2,362 ipm (60 m/min) in all axes and acceleration of 1.2 G, Tongtai’s VTX drilling and tapping centers are designed for high-precision, high-volume machining applications.
Share





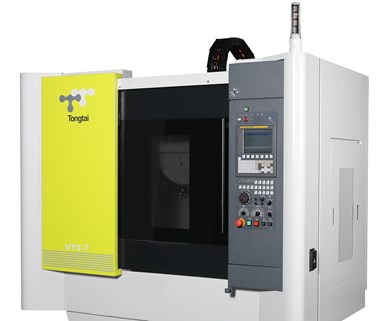
With rapid traverse speeds of 2,362 ipm (60 m/min) in all axes and acceleration of 1.2 G, Tongtai’s VTX drilling and tapping centers — available from Absolute Machine Tools — are designed for high-precision, high-volume machining. A fixed-column/moving-table design with Meehanite cast iron frames and roller-type linear guideways provide rigidity as well as fast, precise movement.
Two types of high-speed automatic toolchangers (ATCs) are available. The 21-tool, turret-type ATC on the VTX-5 and VTX-7 models offers tool change time of 1.4 sec. tool-to-tool and 1.9 sec. chip-to-chip. The VTX-5A and VTX-7A versions have a 20-tool, arm-type ATC that reduces tool change time to 0.8 sec. tool-to-tool and 1.3 sec. chip-to-chip.
The 7.5-hp, 12,000-rpm direct-drive spindle provides rigid tap speeds up to 6,000 rpm. An optional 24,000-rpm direct-drive spindle delivers speeds adequate for machining aluminum, magnesium and graphite parts. A BBT-30 (Big Plus dual-contact) taper suits rigid milling. Coolant through the spindle is standard, as is a spindle chiller.
The Mitsubishi M80A control features a 10.4" (264-mm) touch screen with intuitive smartphone-like operation. A high-response servo system with 1,000,000 pulse encoders increases speed and accuracy. A FANUC OiM-F control with 8.4" (203-mm) LCD screen is also available.
Related Content
-
Inside the Premium Machine Shop Making Fasteners
AMPG can’t help but take risks — its management doesn’t know how to run machines. But these risks have enabled it to become a runaway success in its market.
-
CNC Machine Shop Honored for Automation, Machine Monitoring
From cobots to machine monitoring, this Top Shop honoree shows that machining technology is about more than the machine tool.
-
How to Mitigate Chatter to Boost Machining Rates
There are usually better solutions to chatter than just reducing the feed rate. Through vibration analysis, the chatter problem can be solved, enabling much higher metal removal rates, better quality and longer tool life.