Tungaloy Iso-EcoTurn Inserts Optimize Chip Control
Tungaloy’s Iso-EcoTurn GNMG and FNMG inserts feature reduced nose angles compared to its CNMG and DNMG inserts, improving chip control during certain profile and face turning operations.
Share




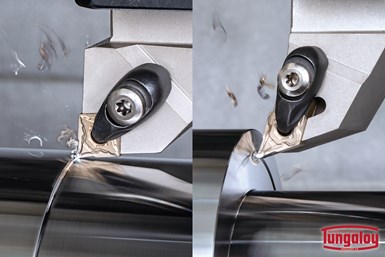
Tungaloy has expanded its Iso-EcoTurn turning insert and toolholders system with GNMG inserts featuring a 70-degree nose angle and FNMG inserts featuring a 45-degree nose angle. This expansion covers a total of 39 additional inserts.
Conventional CNMG or DNMG turning inserts face challenges with chip jamming and re-cutting during profile turning or face turning processes in which the cutting takes place in one continuous path leading away from the work center.
The reduced nose angles of the GNMG and FNMG inserts contribute to lower cutting force, minimizing unpredictable tool failure and chatter during machining. Increased clearance on the cutting edge also allows better chip flow and reduced chip re-cutting issues when face turning walls.
Tungaloy’s GNMG and FNMG inserts include two chipbreaker styles: TM suits general purpose applications, while TSF is optimized for finish turning. The company offers these inserts in T9215 and T9225 CVD grades for steel turning, as well as the AH8015 PVD grade for high-temperature alloys.
As the central bodies of the GNMG and FNMG inserts have identical sizes and shapes to the CNMG and DNMG inserts, users can mount the new inserts to standard turning toolholders for CNMG or DNMG inserts.
Related Content
-
Medical Shop Performs Lights-Out Production in Five-Axes
Moving to five-axis machining enabled this shop to dramatically reduce setup time and increase lights-out capacity, but success relied on the right combination of workholding and automation.
-
Shoulder Milling Cuts Racing Part's Cycle Time By Over 50%
Pairing a shoulder mill with a five-axis machine has cut costs and cycle times for one of TTI Machine’s parts, enabling it to support a niche racing community.
-
The Future of High Feed Milling in Modern Manufacturing
Achieve higher metal removal rates and enhanced predictability with ISCAR’s advanced high-feed milling tools — optimized for today’s competitive global market.